Purpose
The purpose of this article is to help consultants to make an appropriate definition of SAP work centers in the production plant model.
Part 1: Simple production schemes
General Criteria
A production resource (equipment, machine, line, worker(s), etc.) can be defined as a SAP work center if it satisfies at least one of these criteria:
- The resource is a bottleneck of the process (i.e. it has no idle time in production campaign )
- The resource is relevant in costing aspects ( $ /hour is high when compared to other resources)
Of course, one could define some other resources as SAP work center if a better and detailed plant model must be accomplished. The counterpart is that some additional work will be required to maintain master data (Work center, routing or recipes) and to process and confirm production orders. (in general, one can use milestone confirmation but in that case a question arises: why such detail level in work center and operations if a milestone confirmation is to be carried out? )
In the production model and work center definitions some aspect has to be considered:
- Capacity type (Machine or workers)
- Number of capacities
- Work center using Labour from a capacity pool
Some other details as working hours, shift sequence and calendar are assumed to be properly defined to get advantage of this functionality.
As a general rule, one
should avoid defining each person of the crew as a work center (an error frequently found in many implementations) as long as they can perform similar activities.
A definition based on skills is far more valuable (supervisor, skilled worker, apprentice) considering the number of capacities of each skill and linking the work center to HR to assign personnel data to each capacity.
Morphology |
Capacity type |
Nr |
Pool |
Remark |
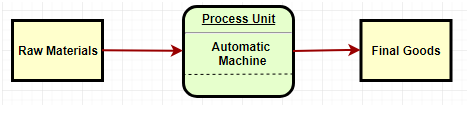 |
Business Case: a packaging machine with a bulk as a raw material and a final product in bags or drums. |
Machine |
1 |
N/R |
Just one work center can be defined. |
 |
Business Case: two automatic machines producing finish goods.
Both machines can process the same products.
Traceability is not required. That means, to identify the physical unit that processes a given production order or batch. |
Machine |
2 |
N/R |
One work center with two machine capacities. |
Machines are suitable for different products or traceability is required. |
Machine |
1 |
N/R |
Two different work centers. |
 |
The unit requires labor to operate. There are two cases, at least, to be considered |
|
|
|
|
- Work force is required during all the operation cycle. |
Machine + Person |
1 |
N/R |
One work center with two capacities |
- During some periods machine runs automatically and the some attention of the operator is required. |
WC Machine
WC Person |
1
1 |
N/R |
Two work center are required |
Additionally, an operator or group of operator can supervise several machines. In that case, you can define each WC as Machine/Person capacity, being Person capacity taken from a pool |
Machine + Person |
1 |
Yes |
One WC with person capacity from the pool. |
 |
The question here if two different WC are to be considered or the use of just one work center is enough for scheduling and costing purposes. It is assumed that two operations (at least) exist in the routing and both machines are required for the production. |
|
|
|
|
Both Machines are similar in costing or residence time |
Machine |
2 |
N/R |
Better result in costing and scheduling. The second production order can be started before the first in finished |
One machine is very fast (low residence time) or not expensive($/hour) in operating costs. |
Machine |
1 |
N/R |
With one work center there is a good approximation to costing or scheduling. |
Conclusions
Some general criteria have presented, mainly related to capacity type (machine or person), numbers of capacities and splitting (or not) a production line into single work centers.
The aim is to represent the production plant with a reasonable set of work center, allowing us to cover the requirements of scheduling, capacity evaluation and costing without falling into a complex listing of (almost) individual work centers.
Coming soon
Part 2: The use of the pool of capacity and the link to HR for planning and confirmation.